Introducing our Dust Sweep (also known as Chip Sweep), 3/4" Bandsaw Blades - available in 1"-1.25" blade widths.
Save time and clear away dust as you saw, for 75% cleaner boards - without the hassle.
Packs of 10, and Full Box
The larger the pack, the bigger the savings - From $15 a blade, with shipping included! Best price anywhere.
For precision cutting in various applications, our
Introducing our 1.25" width, .042 thickness, 3/4" tooth Chip Sweep (Dust Sweep), 144" (12') - 158" (13' 2") All-Purpose Bandsaw Blades, are the ideal choice. Here are the key features:
Precision-Crafted:
These industry-standard carbon steel blades come with a 1.25" width and a 3/4 inch chip sweep tooth design, sweeping dust, chips and debris from your workpiece as it cuts. This configuration ensures up to 70% less cleanup and and helps prevent clogging, for a streamlined workflow.
Versatile Cutting:
Our all-purpose blades are designed to tackle softwoods, hardwoods, and frozen woods, making them suitable for a variety of tasks.
American-Made Quality:
Manufactured in the USA, these blades are built to last.
Wide Compatibility:
These blades fit band saws and portable saw mills and resaws in various makes and models, as well as DIY saws, providing convenience and versatility. Works with brands like Wood-Mizer, Norwood, Woodland Mills, Frontier, Grizzly, Oscar, Harbor Freight, Forest West, Sawyer.
Blade Options:
We offer a variety of blade widths, from 1" to 2", and in dozens of combinations of lengths, tooth width, spacing, and angle, so check out our store page for more options. Need something special? Reach out to us for a custom quote.
Additional Info:
Tooth Spacing, or Pitch:
When we reference 3/4", that's the pitch, which is measured from the gullet to the tooth tip and is determined by the TPI. 7/8" is a good all-around pitch for portable band saws, and most types of wood. 3/4" is for tougher jobs, and Chip (dust) Sweeps come exclusively in the 3/4" configuration.
Types of Wood
The carbon steel blades work with a variety of types of wood -
Softwoods: Softwoods, used most commonly in for construction, are evergreen trees - conifers with permanently attached needles, like cedar, pine, spruce, hemlock, fir and redwood.
Hardwoods: Deciduous trees that lose their leaves in colder months. Species like walnut, maple, beech, cherry, elm and oak are all hardwood trees
Hook Angle:
Hook angle, such as 10/30, is the angle, as seen from the side of the blade, of the cutting face (known as the face angle) of each blade tooth (10 degrees), and the angle of the back of each tooth (30 degrees). Common and general purpose angle combination is 10/30 - 10 degrees of face angle, and 30 degrees of back angle. This spec is good for a variety of softwoods, like yellow pine, spruce and cedar, and hardwoods like oak, walnut and maple.
Tooth set (side set) and best practices:
Tooth set, also known as side set, is the angle as seen from above the blade - a pattern in the tooth set alternates between left, then right, then a straight tooth, and repeats left, right, then straight. This is a common pattern, known as a raker. It determines whether the blade cuts effieciently in your chosen material, or gets clogged with chips. The angle used for these left and right sets are commonly between .0021 - .0022 of inch set, a good general purpose spec.
For working with majority softwoods, like Yellow Pine, a wider tooth set of .0025 will allow extra space for the blade as the softwood expands around the blade, preventing it from pinching. This set can be achieved when re-sharpening blades.
Blade Thickness:
.042 blades - Longer lasting when used with lower horsepower machines of 24HP or less. Best where speed and production is not critical.
.050 and .055 blades - Cuts more efficiently, especially through knotty, frozen, dry or especially dense materials. For machines over 24HP.
Quality Welds:
A note from our manufacturer on our blade welds - "Premature breakage at the weld is not normal. Several weld break testings are performed on a twist test machine throughout each day to ensure top strength quality. We take a welded piece and run it through the twist test machine. We are looking to see if our welds are between 80-90 % of the blade strength.
Often times we get 100%. This means the blade itself breaks before our weld. In those cases, the weld is just as strong as the blade."
If you have any questions about the type of blade you will need, send us a message!

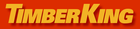

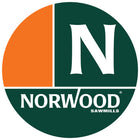
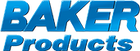
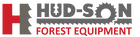

